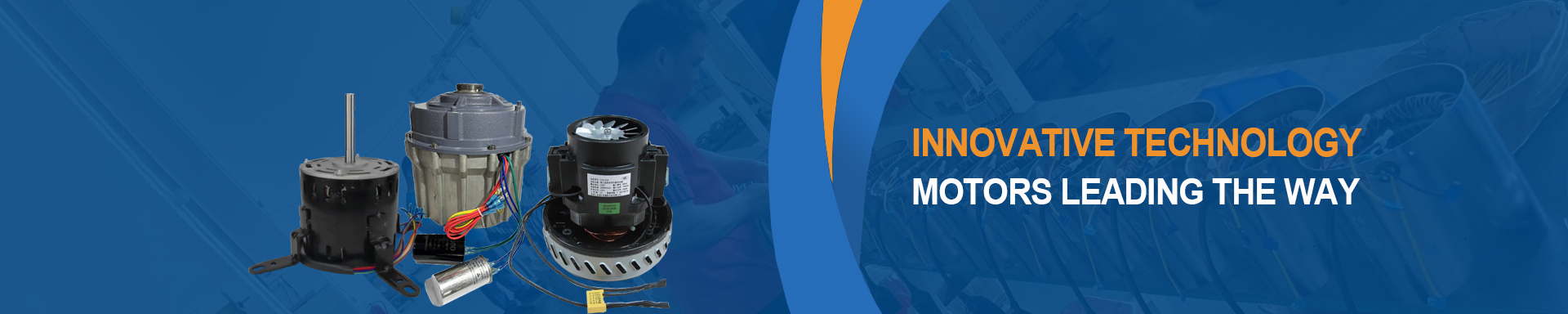
Electric motor technology
2025-05-13 11:30I. Core Application Areas of Motor Technology
Industrial Automation and Manufacturing
Servo motors: They achieve high-precision position and speed control in CNC machine tools and industrial robots, supporting the synchronous coordination of complex movements.
Stepper motors: used in automated production lines, 3D printers and other equipment, directly controlling angular displacement through digital pulse signals, simplifying the design of control systems.
◦ Brushless DC motors (BLDC): Due to their high efficiency and low maintenance requirements, they are widely used in industrial pumps, fans, and automation equipment.
2. Transportation and Logistics
Electric vehicles: Permanent magnet synchronous motors (PMSM) and switched reluctance motors (SRM) have become the core drivers due to their high power density and long driving range. At the same time, auxiliary equipment such as electric power steering and braking systems also rely on efficient motors.
◦ Rail transportation: Linear motor technology is applied to maglev trains and metro drive systems, enhancing operational efficiency.
3. Consumer Electronics and Home Appliances
Miniature motors, such as brushless DC motors and stepper motors, are used in household appliances like air conditioners, refrigerators, and washing machines to achieve low noise and energy-efficient operation.
Intelligent devices such as drones, power tools, and smart toys rely on micro-motors for operation, which require high energy density and rapid response.
4. Medical equipment
Precision control: Motors in surgical robots and MRI equipment must meet high-precision and low-vibration requirements. Brushless motors and piezoelectric ceramic motors are typical choices.
Auxiliary equipment such as ventilators and infusion pumps rely on miniature permanent magnet motors to ensure long-term stable operation.
5. National Defense and Special Fields
Military equipment: Rare earth permanent magnet brushless motors are used in torpedo electric steering gear, unmanned aerial vehicles, etc., to enhance reliability and dynamic performance.
Extreme environment applications: High-temperature resistant and radiation-resistant motors are used in spacecraft and deep-sea probes, supporting operations in special environments.
II. Development Trends of Motor Technology
High Efficiency Energy Conservation and Material Innovation
High-efficiency motor grades: IE3 and IE4 standard motors are gradually becoming widespread. Energy consumption is reduced by optimizing the winding design and using high-performance magnetic materials (such as nanocrystalline soft magnetic alloys).
◦ Rare earth alternative materials: Develop rare earth-free permanent magnetic materials (such as manganese-aluminum-based magnets) to reduce reliance on rare earth resources.
2. Intelligence and Digitalization
Intelligent diagnosis and predictive maintenance: By integrating sensors and Internet of Things (IoT) technology, the operating status of motors is monitored in real time to achieve early warning of faults and remote maintenance.
Digital twin technology: Optimize motor design through virtual models to enhance control accuracy and energy efficiency.
3. Brushless Technology and Integration
◦ Brushless DC motors (BLDC): Replacing traditional brushed motors in high-end household appliances and electric vehicles, they enhance efficiency and lifespan.
Mechatronic design: Integrating motors with drivers and controllers to reduce size and enhance system reliability.
4. Expansion of Emerging Application Scenarios
Electric aviation: Superconducting motors and distributed electric drive systems facilitate the development of electric aircraft and drive the decarbonization of the aviation industry.
Micro-robots: Piezoelectric drive motors and micro-permanent magnet motors are applied in medical endoscopes and micro-detectors.
5. Green Manufacturing and Sustainable Development
Environmentally friendly materials: Utilizing recyclable plastics and low-pollution manufacturing processes to reduce carbon emissions during production.
Recycling of waste motors: Establish a circular economy system to enhance the recycling and utilization rate of rare earth materials.
III. Challenges and Future Prospects
• Technical bottlenecks: The shortage of rare earth resources and the high difficulty in the practical application of superconducting materials remain constraining factors.
Cost control: The large-scale production of high-performance motors (such as permanent magnet synchronous motors) needs to further reduce costs.
Standardization requirements: Promote the unification of global motor energy efficiency standards to facilitate technological compatibility and market expansion.
In the future, motor technology will focus more on efficiency, intelligence and greenness, and play a more crucial role in fields such as new energy, intelligent manufacturing and healthcare. With the deep integration of new materials and artificial intelligence, motor systems will evolve towards higher performance and greater flexibility.